Latest News
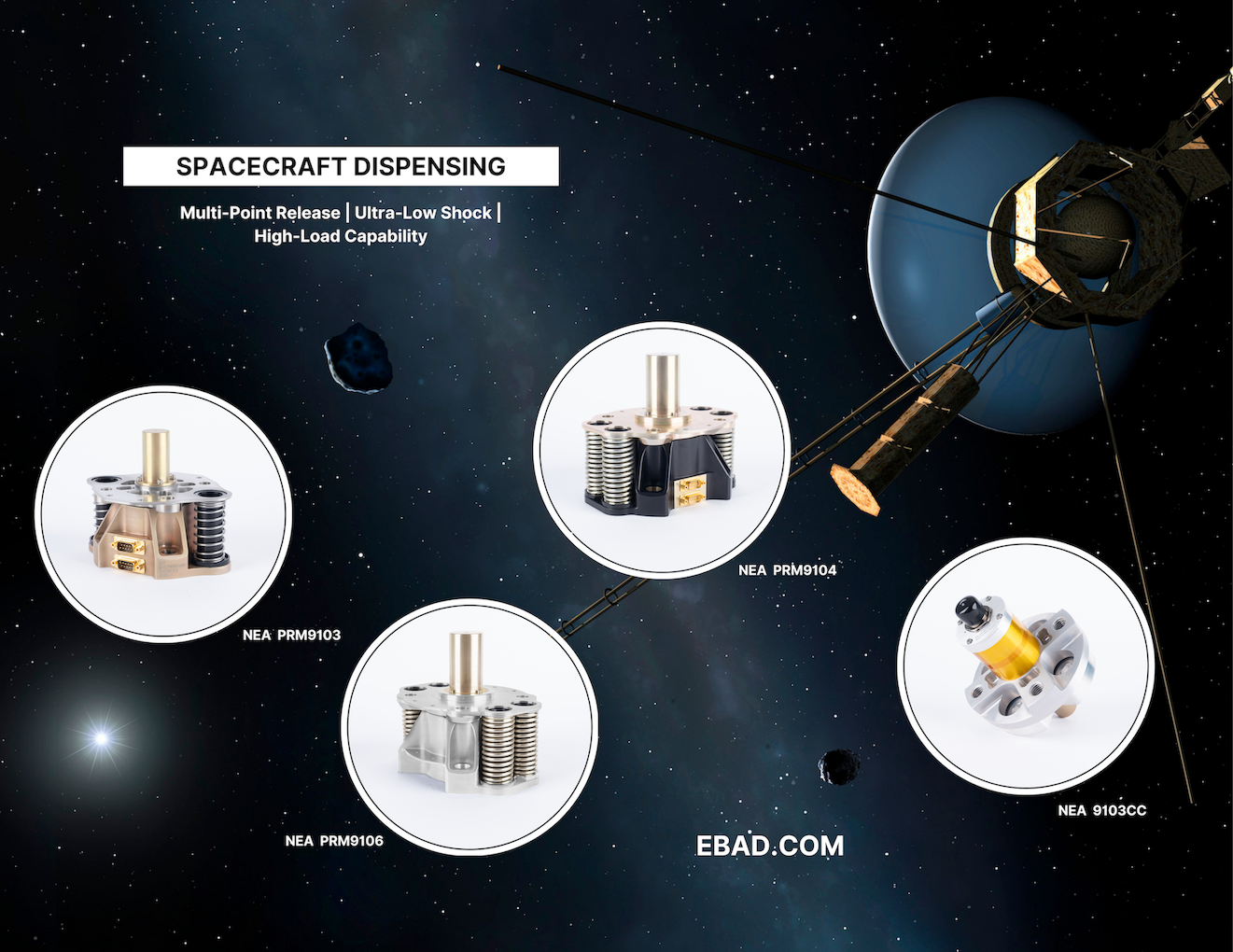
EBAD’s spacecraft dispensing technology. Photo: EBAD
Launch day is a nail-biting experience for spacecraft operators and manufacturers watching on the ground as thousands of dollars in investment is rocketed to space. While launch vehicles tend to get the most attention, there are many critical components that help spacecraft reach their final orbital destination safely.
Manufacturer Ensign-Bickford Aerospace & Defense (EBAD) provides payload dispensing systems that ensure spacecraft reach orbit intact with precision and reliability. EBAD recently achieved a major milestone of qualifying its NEA® Payload Release Module™ (PRM) to meet SpaceX’s Falcon 9 Rideshare Payload User’s Guide (RPUG) requirements. With this qualification, EBAD’s PRM™ is one of the few systems aligned with SpaceX’s benchmarks for low risk, low-shock, redundant, and precise separation systems.
The PRM™’s 4-point release mechanism is part of a shift away from ring dispensing systems to multi-point dispensing systems, as spacecraft manufacturers and operators seek more flexible design options.
The PRM™ works by securing the spacecraft to the launch vehicle, and on command, reliably releases the spacecraft into orbit. It secures the satellite to the launch vehicle as it handles the extreme loads during launch. The PRM™ has integrated and adjustable push of springs to release the spacecraft with the correct separation velocity, and it comes with telemetry switches to provide separation signals to confirm once separation has occurred. The system is delivered fully preloaded, and no custom tools or on-site training are required for installation, making integration into space platforms simple and efficient.
An Evolution Backed by Flight Heritage
EBAD has deep heritage in space mechanisms. The company’s hold down release mechanism (HDRM) brands, NEA® and TiNi™, are widely accepted as the industry standard. The NEA® is the primary release element of the PRM™.
Mike Ronzello, EBAD’s director of Strategy and Business Development, calls the NEA® the “household brand” of the industry because the category is often defined by the NEA® product name. The NEA® goes back more than 29 years and has nearly 10,000 releases in space with zero failures.
In two particularly notable examples of its flight heritage, the NEA® supported the James Webb Space Telescope with 178 NEA® mechanisms. The NEA® was responsible for holding the entire spacecraft in its launch configuration during ascent, and through various deployment events while the spacecraft unfolded. The NEA® also supported the European Space Agency’s Rosetta mission to rendezvous with a comet, where the NEA® successfully released in space seven years after launch.
“The NEA® was selected by Northrop Grumman and NASA for James Webb because of its extensive heritage and its reliability,” Ronzello said. “These were single point failure devices — meaning if one NEA® were to have problems, then the mission would have been significantly compromised. Customers can be confident in the PRM™ from a reliability standpoint.”
Ronzello explains how in recent years, EBAD observed a shift in spacecraft, with changes in propulsion and spacecraft design. In the past, spacecraft were often circular because liquid propulsion tanks are circular, making the nozzles circular as well. As more spacecraft use electric propulsion, it challenges the notion that spacecraft must be round, and leads to more flexible designs.
This led the company to build on the heritage of the NEA® and create the PRM™.
“We saw a transition in the market. Payloads were getting more sophisticated and requiring more power. More power means larger spacecraft, and larger spacecraft means higher loads that have to be managed,” Ronzello said. “There’s a shift in the market from the traditional circular dispensing systems, which have limitations on how much load they can react. We saw those limitations being reached, and we presented a unique solution to the market with multi-point dispensing.”
He explains that as spacecraft are now built in various shapes and sizes depending on the mission and the payloads, a multi-point dispensing mechanism gives customers the flexibility in how spacecraft loads are distributed and mounted to the launch vehicle.
“This is different from the traditional approach of a circular ring where you are constrained to certain size standard rings and you have to somehow design your spacecraft around those standards,” Ronzello said. “Now, that constraint is eliminated and you can design your spacecraft based on the mission — not based on a standard circular interface.”
Philip Venti, director of Satellite Systems for EBAD, said when the product was in development, EBAD talked with customers about adapting the NEA® to put the bases on corners instead of a circular formation. During these discussions, one customer had a site visit in two weeks and wanted to see a prototype.
EBAD quickly created a fully functioning metal prototype ready for the customer’s visit. The customer signed on for the first version of the product and the product flew on the Transporter-9 rideshare mission in 2023. It was designed, qualified, and flown within just 10 months, an impressive pace for hardware development.
Since then, the PRM™ has gone from one order to many orders and is expected to have 100 releases in space by the end of this year. The product has been selected to support multiple commercial constellations, and the Space Development Agency’s space layer constellation.
“It’s in the right place at the right time,” Venti said. “There’s nothing else on the market that integrates all of this hardware — the shear interface, the springs, various telemetry, built into one package that you can put in the corners, or wherever the customers want to put it on their spacecraft.”
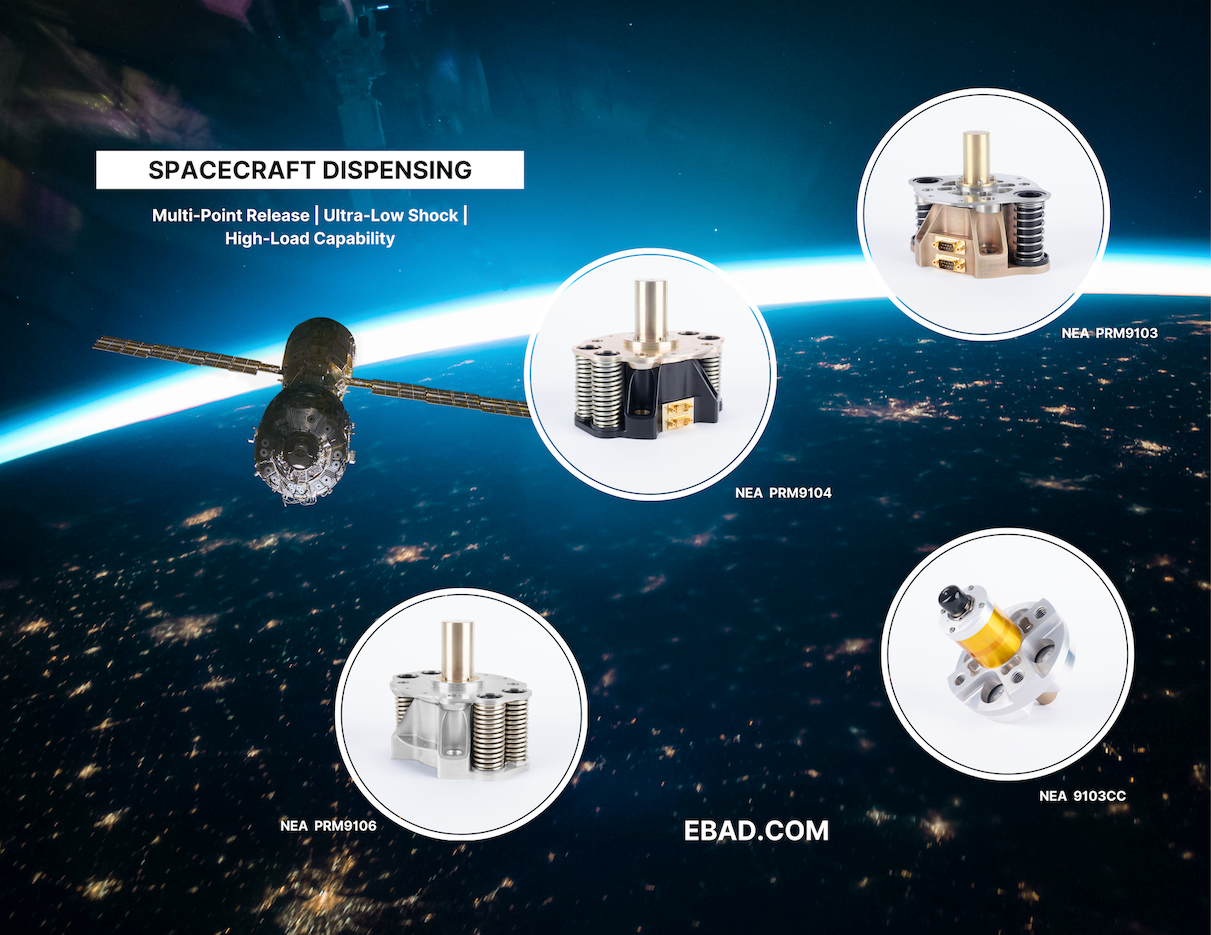
EBAD’s spacecraft dispensing technology. Photo: EBAD
A Plug and Play Solution
Two PRM™ sizes are currently qualified to support smallsats from 100 kilograms to about 1000 kilograms. EBAD is also developing a PRM™ that will support up to 2,000 kilogram spacecraft in a four-point configuration, and has plans to design a PRM™ that uses the largest NEA® to handle up to 40 metric ton satellites.
The PRM™ is a fit for missions to any orbit – Low-Earth Orbit (LEO), Medium-Earth Orbit (MEO), Geostationary Earth Orbit (GEO), and beyond, on both rideshare missions and dedicated launches.
In addition to the qualification for SpaceX’s Falcon 9 Rideshare Payload User’s Guide (RPUG) requirements, the PRM™ is compatible with all current and upcoming launch vehicles including United Launch Alliance Vulcan Centaur, Blue Origin’s New Glenn, and Rocket Lab’s Neutron vehicle, in addition to Orbital Transfer Vehicles (OTVs) that are gaining momentum
Michael Creaven works closely with EBAD’s customers in his role as principal systems engineer. He explains how EBAD built a plug-and-play solution around the NEA® to make it more simple for customers.
“We made it customizable for customers, so they can simply bolt it on and go,” Creaven said. “The engineering is already done, and they don’t have to do all the development effort, all the sizing, qualification, all of that Because there are single modules, you can place them anywhere you want. It’s a really nice plug-and-play option for customers.”
Creaven notes one of the things customers really like about the PRM™ and NEA® is that it is very low shock, making it very attractive to customers whose satellites have sensitive electronics or optical equipment onboard.
Venti added that customers can choose their spring force from a number of sizes, or customers can specify their own springs which can be modified after the hardware is delivered. If a customer has last-minute changes to the spacecraft payload that impacts the center of gravity, they can make adjustments to the springs to accommodate.
For large constellations, Ronzello said the PRM™ significantly reduces the handling, transportation, and integration logistics by having a standard unit delivered in a turnkey package, with no unique procedures necessary to align to the spacecraft. Ronzello said large constellations have selected the PRM™ because it can simplify their logistics.
“When we’re talking about large constellations with repeat mounting and assembly, the PRM™ significantly reduces the handling and integration logistics. This ultimately reduces complexity and cost,” he said.
An Emphasis on the Customer
EBAD is a high volume, full rate production operation with extensive in-house manufacturing capabilities. The company has dedicated work cells for the PRM™. All of the critical components are made in-house with materials that are made in the United States.
Lead times for the PRM™ are typically shorter than traditional dispensing systems and Ronzello said EBAD is working on even further improvements to delivery times to satisfy the ever changing requirements in the smallsat world and give customers more flexibility.
“If long lead times force customers to order early, it eliminates flexibility when they learn things through testing as their design matures,” he said. “EBAD is focused on reducing lead times so customers are not locked into a design and procurement decision too early.”
In addition, many PRM™ customers need responsive customer support and EBAD has a long history of working custom designs with ever changing requirements. The company offers engineering and test services as well.
As a privately held company that was founded in 1836 that has been in business for 189 years, Ronzello stressed that EBAD is focused on long-term decision-making, which is reflected in its values and how it works with customers.
“We have an experienced team of both leadership and technical operations that work together to be the standard for the industry. People trust EBAD because of our technical expertise, ability to deliver, our quality, and our customer support,” Ronzello said. “We have a tremendous focus on supporting the customer and making sure that we’re helping them achieve their mission. At the end of the day, that’s what we are here to do.”
Get the latest Via Satellite news!
Subscribe Now