Latest News
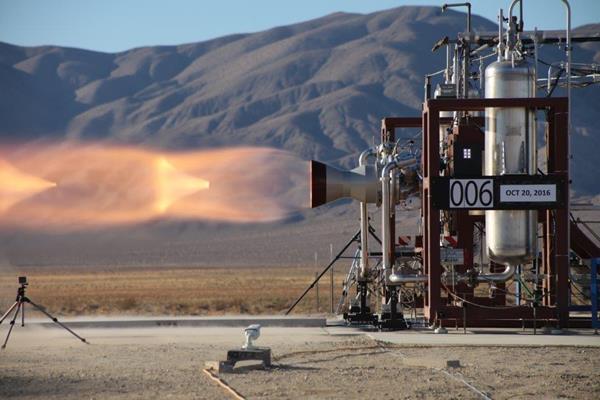
Hot-fire tests on two Launch Abort Engines for Boeing’s CST-100 Starliner service module propulsion system. Photo: Aerojet Rocketdyne
[Via Satellite 11-01-2016] Aerojet Rocketdyne announced it has successfully completed a series of hot-fire tests on two Launch Abort Engines (LAE) featuring new propellant valves for Boeing’s Crew Space Transportation (CST)-100 Starliner service module propulsion system. The tests were conducted in the Mojave Desert in California, and confirmed the ability for the new valves to modulate propellant flow and control peak LAE thrust in the event of a launch abort.
The LAEs, designed by Aerojet Rocketdyne, include a fuel valve and oxidizer valve, which were developed and tested under the company’s Commercial Crew Transportation Capability (CCtCap) subcontract to Boeing. The Starliner aims to carry humans to the International Space Station (ISS) once again from United States soil.
The Starliner service module propulsion system provides launch abort capability on the pad and during ascent, along with propulsion needs during flight — from launch vehicle separation, docking to and undocking from the space station, to separation of the crew and service modules when the spacecraft begins to re-enter the Earth’s atmosphere. At separation, crew module monopropellant thrusters, also provided by Aerojet Rocketdyne, support re-entry control.
The Starliner service module and launch abort propulsion system is designed to rapidly “push” a crew capsule to safety if an abort is necessary. If unused for an abort, the propellant is used to complete the spacecraft’s mission operations.
Get the latest Via Satellite news!
Subscribe Now